An essential part of fire risk management
For these reasons, hydrocarbon passive fire protection (PFP) coatings are an increasingly important part of hydrocarbon fire hazard management and risk management on power generation and oil & gas facilities around the world, including oil refineries and downstream processing plants.
What are passive fire protection coatings?
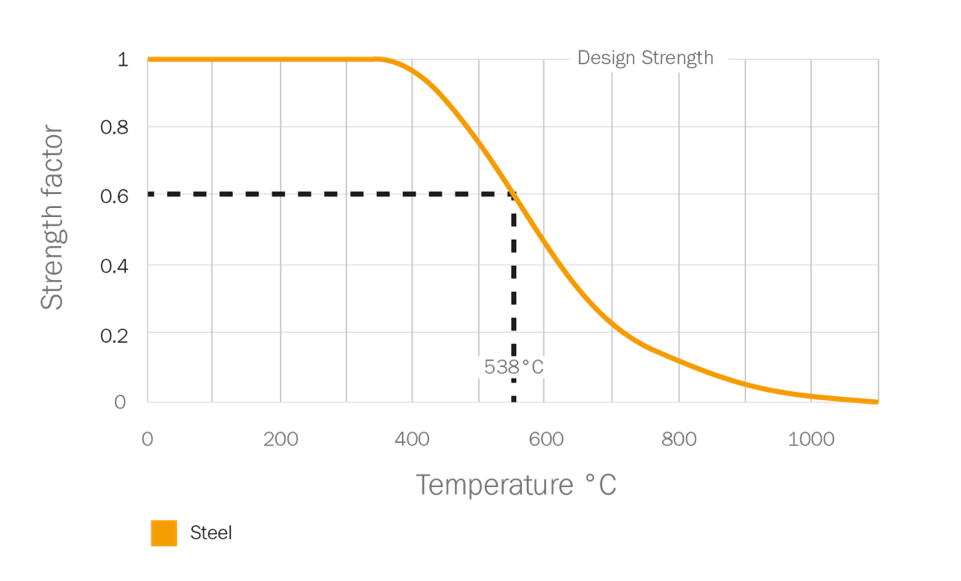
PFP coatings are applied to structural steel. When exposed to the high heat of a fire, the PFP coating swells to form an insulative layer, which enables the steel to maintain its load-bearing capacity for up to four hours. As passive fire protection systems, PFP coatings are designed to contain and minimise the effects of a fire. They do not stop fires breaking out. However, they give valuable extra time for the evacuation of personnel and minimise damage to assets while firefights put out the fire.
How hydrocarbon passive fire protection coatings can lower project costs
Hydrocarbon PFP coatings are applied to a range of steel structures within energy generation and oil & gas facilities, including structural steel (beams, collars, bracings and coatbacks, etc.), pipe racks and vessel supports (skirts, saddles, legs, etc.). They have a number of advantages over other passive fire protection systems used in the energy generation and oil & gas industries. They are, for example, lighter and easier to apply than cementitious products, which leads to significant time and cost savings during application, transportation and maintenance.
To further reduce project costs, high-efficiency hydrocarbon PFP coatings are available. These coatings offer the same performance as standard hydrocarbon PFP coatings at lower dry film thicknesses (DFTs), which reduces product costs, labour costs and application time, and therefore reduces overall project costs. On a large construction or maintenance project, a high-efficiency coating, such as Hempel’s Hempafire XTR 100, can save owners and asset operators considerable time and expense.
How passive fire protection coatings work
PFP coatings are reactive intumescent paints. When exposed to higher temperatures a series of decomposition mechanisms and physical processes happen. These include the release acid above 150°C and the esterification of carbon-rich compounds above 250°C. Due to the released gases, the material carbonises and the coating begins to swell, forming a so-called ‘char’ that is 5-10 times the thickness of the original coating.
This char insulates the steel by decreasing the rate of heat transfer from the fire to the steel.
The length of time that a PFP coating will protect the steel is known as the ‘fire duration’. This varies from 30 minutes to four hours and is determined by a number of factors, including the type of coating and the applied DFT.
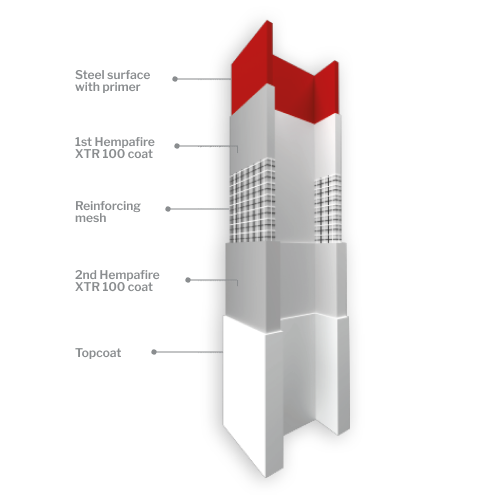
Protection against the high heat of hydrocarbon pool fires
When selecting a PFP coating system, a number of factors must be carefully considered, including project efficiency requirements. However, the most important consideration is the type of fire that the coating may be exposed to.
There are three main types of fire, which burn at different temperatures depending on the material. At power generation and oil & gas facilities, hydrocarbon pool fires and hydrocarbon jet fires are more common. These generate more heat than cellulosic fires and, as a result, especially designed hydrocarbon PFP coatings are required in these facilities. As well as the high burning temperature, hydrocarbon pool fires can generate heat fluxes above 150 kW/m2. Jet fires tend to be more localised, but heat fluxes may be twice as strong.
-
Cellulosic fires
Flammable material:
Wood, textiles, paper, etc. Fire temperature: 800-950°C Area: Civil construction, such as office buildings, factories, transportation hubs and office blocks
-
Hydrocarbon pool fires
Material:
Oil & gas fuels Fire temperature: Up to 1100°C Area: Power generation, oil & gas and petrochemical industries
-
Hydrocarbon jet fires
Flammable material: Compressed oil & gas fuels Fire temperature: Up to 1200°C Area: Oil & gas and petrochemical industries
Certification and specification
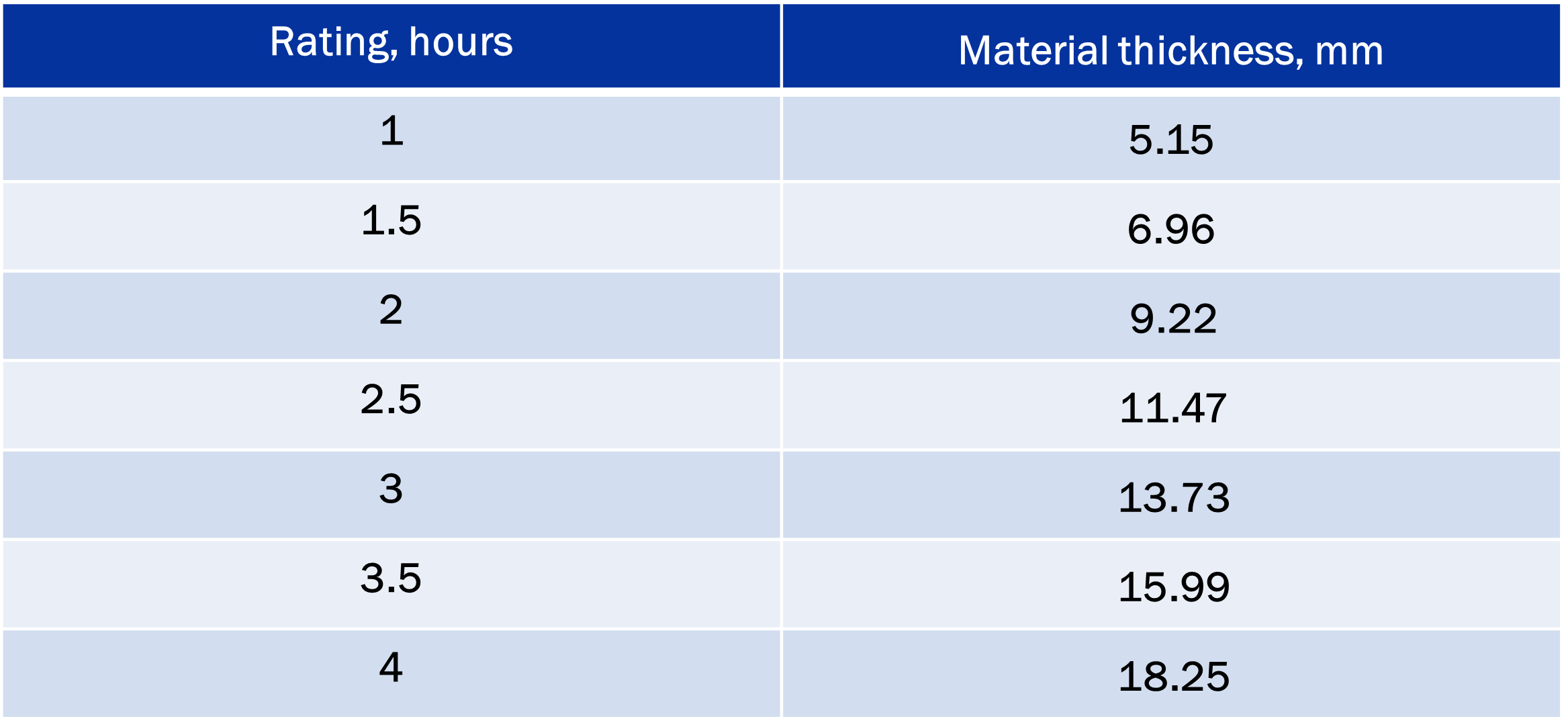
When selecting a hydrocarbon PFP coating system, many factors need to be taken into account, from the application conditions to the type of fire and required fire duration. It is also essential that performance in the end-use environment is considered. For these reasons, consultation with the manufacturer is strongly recommended
In order to select the correct hydrocarbon PFP system for your project and end-use environment, get in touch with your local Hempel office.