Executive summary
Up until the recent downturn in the oil and gas industry the previous decade saw unprecedented levels of new construction projects across many industry segments, oil & gas, power generation and infrastructure as well as many others.
Protective coatings are often the primary means of corrosion control for many such projects – driven by the need to protect large steel structures efficiently and to provide effective long-term protection. Whilst this often is at the forefront of the design and specification process, maintaining long-term performance can be challenging when faced with compressed project schedules where painting is seen as a “necessary evil”.
This is where faster drying coating systems can be utilised to improve the productivity of the painting process particularly if each component layer of a coating system is faster to dry and overcoat with the next layer. Whilst this may seem an attractive option, it must be carefully balanced against maintaining the long-term integrity of the coating system, which is increasingly called upon to last for longer and longer periods.
Why paint fast?
Painting is often seen as a late stage activity that it is completed at the very end of the fabrication or construction cycle:
- When applied on site painting is definitely one of the last things on the list, and as such the timeframe to complete it is often under pressure as start-up / commissioning approaches.
- When carried out at the fabrication stage, painting is often the last activity after welding and other shop or yard activities are completed, and when the pressure is on to move coated sections quickly to make way for the next project.
- When applied to smaller component items painting takes place after mechanical completion and before components can be shipped, which again creates an urgency to speed up the process.
What drives productivity in a painting process?
Whilst many factors can influence the productivity of the painting process, these can be separated into a number of key areas:
- The availability of suitably prepared steel, type of painting equipment, manpower levels, shop configuration, degree of inspection activity etc.
- The properties of the paint system such as the number of coats, the coating dry film thickness (DFT) specified, percentage of volume solids, drying time, minimum overcoating time, amongst others.
- The environmental conditions at the application location at the time of painting:
(i) Physical drying, and in the case of chemical cure such as is found in two-component systems e.g. epoxies, is dependent upon the temperature when application takes place and is subsequently exposed. In the case of solvent based schemes ventilation may also be an influencing factor.
(ii) Other systems which rely on moisture to assist their cure, such as zinc silicate primers can be humidity dependent and therefore painting progress slows in locations with low relative humidity. In some cases forced wetting of the primer is required to limit this impact on productivity.
In a multi-layer paint system different properties can speed up the productivity of the coating system. Looking at a typical three-layer coating scheme such as would be used for structural steel in a coastal or offshore environment, reducing the minimum overcoating time in the initial two layers can have a significant effect on productivity. Whereas for the final coat the focus is on ensuring that the paint systems develop sufficient mechanical properties to allow it to be handled more quickly without damage.
The schematic (down below) shows how reducing the overcoating time of one of the layers of a three-layer paint system can provide significant improvements, with positive benefits to the steel fabricator and to the project schedule.
Typically when comparing different coating systems a more limited view is often taken by only looking at the products drying time, but rarely does this show the complete picture especially when this can be also be heavily influenced by environmental conditions from one location to another.
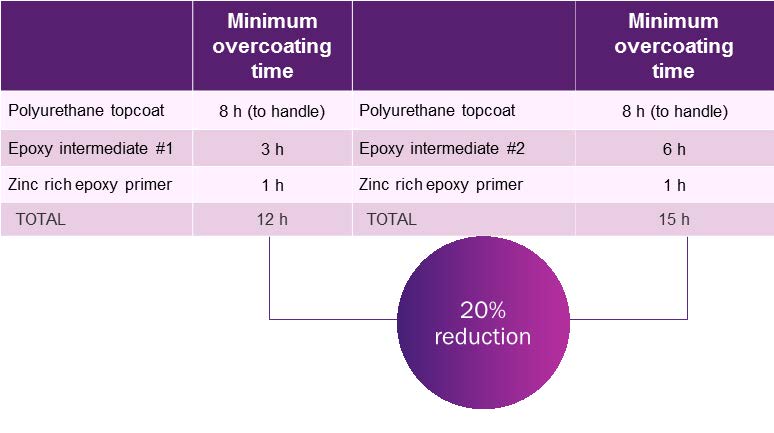
How is coating performance affected?
The development of faster curing, higher productivity painting systems may have an impact on their performance. This is dependent upon a number of factors and the following should be noted:
- When producing faster curing two pack products, the speed of cure must be balanced with the ultimate mechanical properties of the coating system.
- Excessive speed of curing can result in a coating film which is less resistant to cracking, subsequently reducing long-term corrosion performance.
- Cracking is more noticeable in higher film thicknesses which are typically encountered during practical site application than may be described in the specification.
Cracking or splitting failure in a coating system can occur in any layer of the coating system. This, of course, only represents a potential corrosion threat if it penetrates the coating and reaches the steel substrate or is likely to do so within the expected lifetime of the coating, thus requiring earlier than expected maintenance.
To ensure that designers in the specification and designs stage achieve the correct performance for the desired corrosive environment, designers often refer to international standards as recommendation for type, minimum film thickness and number of layers. Standards such as ISO 12944-5 : 2007, ISO 20340 : 2009 and NORSOK M-501 : Edition 6 are in common use across a number of industrial segments. Both ISO 12944 and ISO 20340 are currently under review.
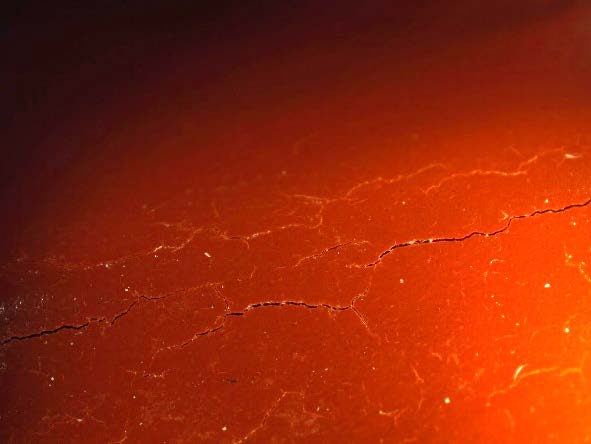
Left: A typical splitting failure of a Fast drying epoxy applied at 300 - 400 microns.
Table 1 (below) shows a except from two of the commonly found standards ISO 12944-5 : 2007 and ISO 20304 : 2009
Table 1: Typical paint scheme thicknesses found in commonly used standards
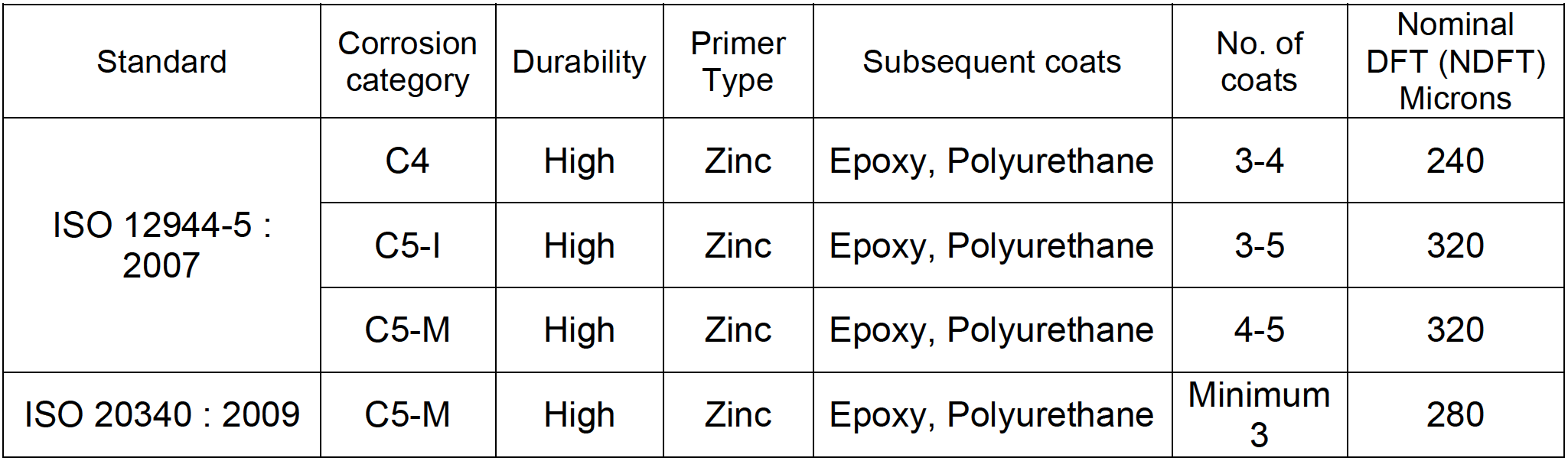
Whilst standards, specifications and manufacturers guides often quote minimum or recommended film thicknesses, the reality of industrial painting, particularly on complex geometries such as structural sections, is that over-thickness is common.
As such it is essential to understand how a coating system will perform not just at its recommend dry film thickness but also at thicknesses above this. A well-constructed specification will list minimum (usually 80% of recommended DFT) and maximum film thicknesses for the avoidance of doubt. ISO 12944-5 defines the maximum film as “the highest acceptable dry film thickness above which the performance of the paint or the paint system could be impaired”. It offers additional guidance that suggests that the maximum dry film thickness is not greater than 3 x the nominal dry film thickness for the avoidance of doubt.
Increasingly designers are becoming aware of the effect of over-thickness and building this in to their pre-qualification requirements. From Table 1 it is possible to see that the highest layer thickness and therefore the one most likely to result in over-thickness should be the intermediate epoxy layer.
Table 2 (below) shows a sample of epoxy paint systems, which are in common use as intermediates after being evaluated for cracking resistance. The evaluation was carried out on test samples following cyclic temperature exposure from + 60°C to -30°C for a period of 21 days as described in NACE TM0404 : 2004 : Section 9.2
Table 2: Effect of recommended DFT and two times the recommended DFT on cracking resistance of a single layer of fast drying epoxy following thermal cycling (NACE TM0404 : 2004 : Section 9.2)
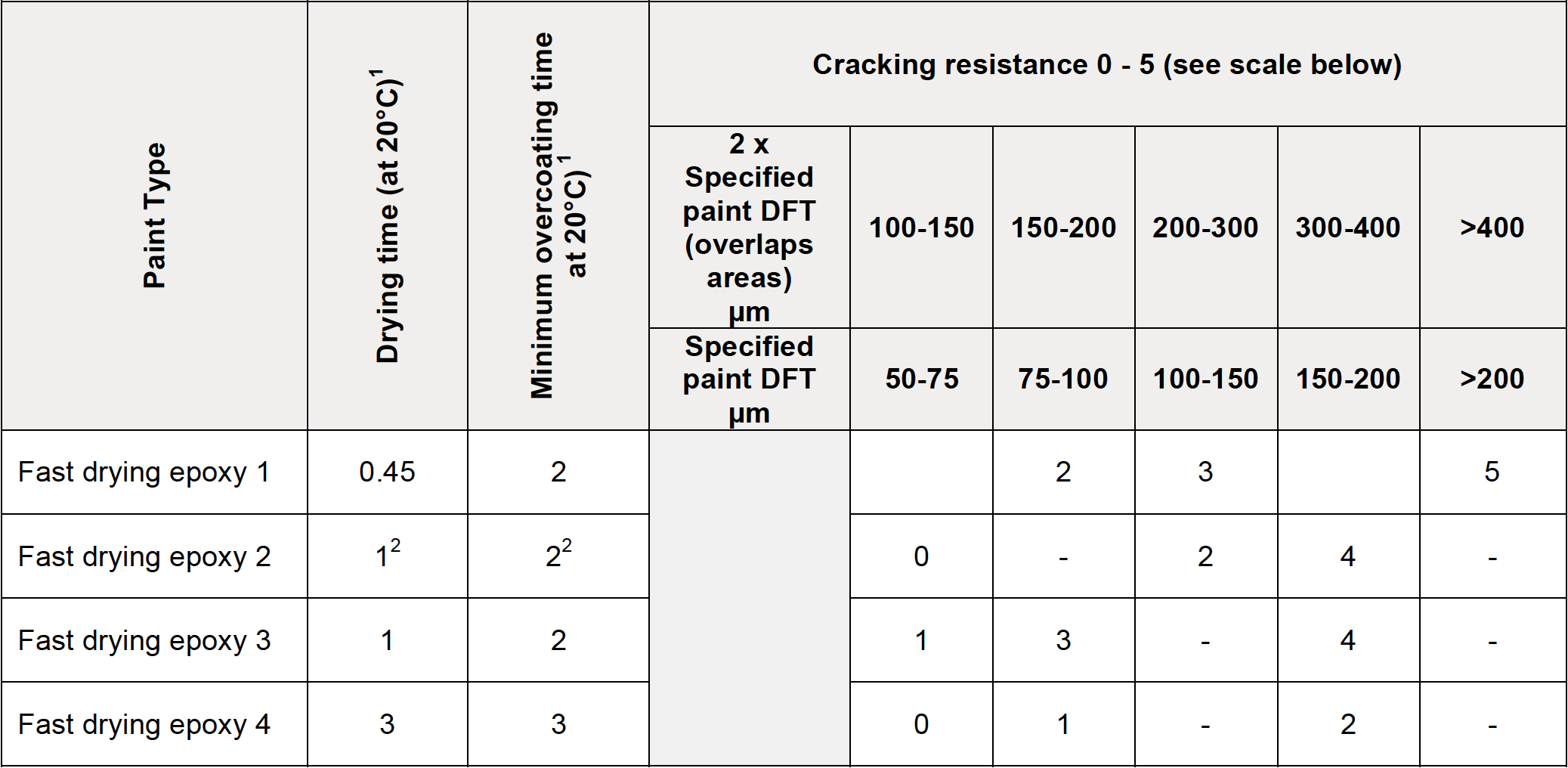
0- No cracks observed with the microscope
1-Superficial cracks observed with the microscope. Steel protection not compromised
2- Cracks observed with the microscope but not with the naked eye. Steel protection not compromised
3- Small cracks visible with the naked eye. Steel protection unlikely to be compromised
4- Continuous cracks visible with the naked eye – Steel protection compromised
5- Continuous and deep cracks visible with the naked eye – Evident coating failure
1 According to online available Product Datasheet
2 Measured at 23 °C
Table 3 (below) repeats the best and worst performing systems from the above evaluation when applied over a layer of zinc rich epoxy primer at a recommended DFT of 100 microns.
Table 3: Effect of recommended DFT and two times the recommended DFT on cracking resistance of a single layer of fast drying epoxy applied over a zinc epoxy primer following thermal cycling (NACE TM0404 : 2004 : Section 9.2)
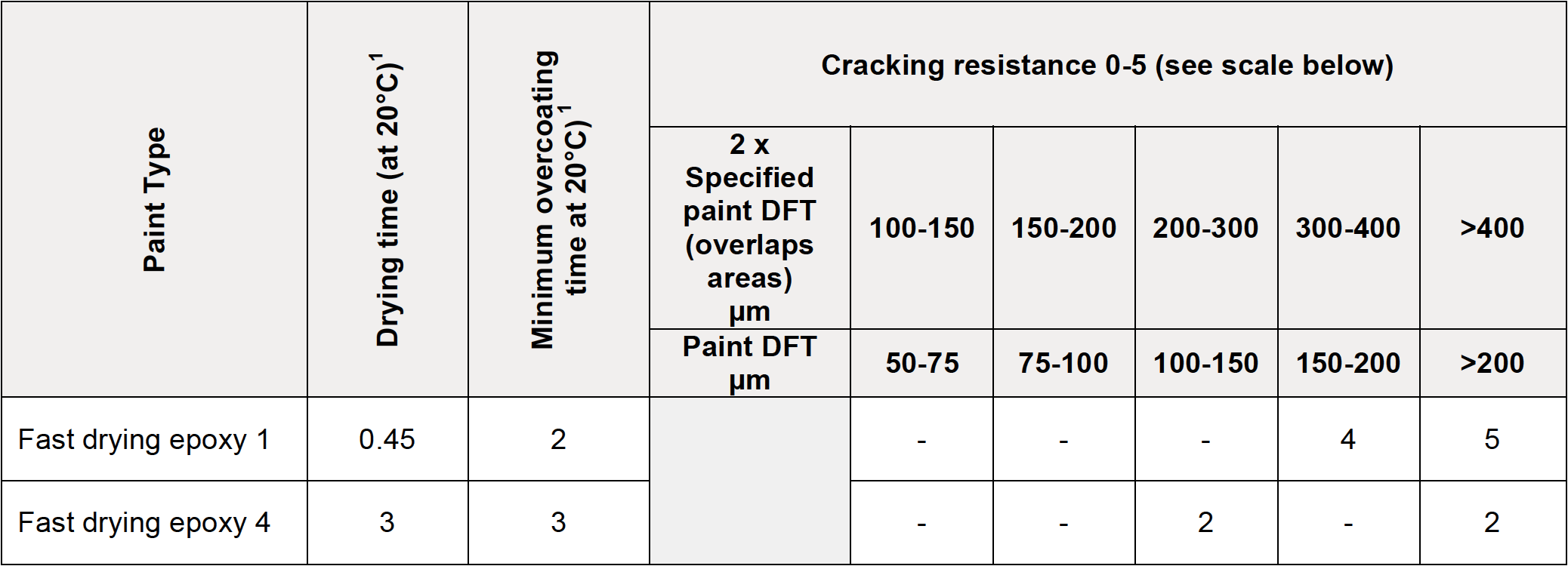
0- No cracks observed with the microscope
1-Superficial cracks observed with the microscope. Steel protection not compromised
2- Cracks observed with the microscope but not with the naked eye. Steel protection not compromised
3- Small cracks visible with the naked eye. Steel protection unlikely to be compromised
4- Continuous cracks visible with the naked eye – Steel protection compromised
5- Continuous and deep cracks visible with the naked eye – Evident coating failure
What can we conclude?
The above works demonstrates that while having significant benefits to improving the speed of curing of the paint material, there are also challenges to the long-term performance. This needs to be balanced when seeking productivity gains.
Additionally it demonstrates the need for greater understanding of the effects of over-thickness with certain product types whereas historically the main focus has been on avoiding under thickness as the key means to providing long term corrosion protection.
About Hempel high productivity coatings
Hempaprime Multi 500 is a high-performance epoxy primer and intermediate which has been developed to offer improved productivity in painting applications.
Furthermore it has been developed to integrate seamlessly with Hempel’s range of Avantguard activated zinc epoxy primers. These primers as well as offering superior corrosion protection have rapid overcoating intervals as short as one hour whilst being highly tolerant to a range of film thicknesses.